با تلاش جمعی مدیریت و کارکنان فولاد مبارکه به ثمر رسید؛ تولید تختال فولاد زنگنزن «آستنیتی» گرید ۳۱۶ برای اولین بار در کشور
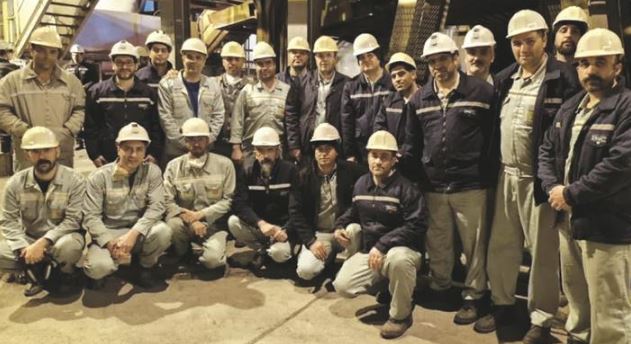
با تلاش جمعی مدیریت و کارکنان فولاد مبارکه، بار دیگر راهبرد تولید فولادهای خاص در این شرکت و این بار با تولید تختال فولاد زنگنزن «آستنیتی» گرید ۳۱۶ برای اولین بار در کشور به ثمر رسید.
در پی کسب این موفقیت، برخی از رؤسا و کارشناسان ناحیه فولادسازی و ریختهگری مداوم در مصاحبه با خبرنگار فولاد چنین گفتند:
محمدعلی شفیعی، رئیس گروه فنی ناحیه فولادسازی و ریختهگری مداوم:
پس از موفقیت در تولید تختال گرید ۴۰۹ و ۳۰۴ در شرکت فولاد مبارکه، پولادمردان خستگیناپذیر در ناحیه فولادسازی و ریختهگری مداوم، با عنایت خداوند متعال با تولید تختال فولاد آستنیتی گرید ۳۱۶ در یکی از سردترین روزهای سال، گرمای ویژهای به مجموعه فولادی کشور بخشیدند.
این موفقیت در حالی به دست آمد که تجهیزات و امکانات موجود در ناحیه فولادسازی و ریختهگری مداوم برای تولید این نوع گریدهای پرآلیاژ طراحی نشدهاند و کارکنان توانمند این ناحیه با همکاری واحدهای پشتیبانی با دانش فنی و خلاقیت، موفق به تولید تختال یکی از پرمصرفترین و پرآلیاژترین گریدهای فولاد زنگنزن شدند. فولاد زنگنزن ۳۱۶ کاربرد ویژهای در صنایع مختلف دارد و مقاومت به خوردگی بالایی در محیطهای کاری کلریدی، اسیدی ملایم و آلوده دریایی دارد. گفتنی است تولید تختال فولادهای زنگنزن اولین گام در جهت تولید ورقهای زنگنزن است و در ادامه، جهت بومیسازی این محصولات در کشور باید فرایندهای نورد گرم و نورد سرد برای این منظور در کشور توسعه یابند.
محمد فخری، رئیس تولید ریختهگری:
در راستای تکمیل سبد محصولات شرکت، گرید ۳۱۶ نیز با موفقیت تولید و ریختهگری شد. پس از تولید ذوب این گرید، ریختهگری آن با تنظیم پارامترهای مهم ماشین ریختهگری مداوم مانند سرعت ریختهگری، شدت خنککاری و تنظیمات مربوط به عرض و اسیلاتور و تأمین پودر قالب مخصوص انجام شد. در حین ریختهگری مداوم، کلیه پارامترهای ذوب و ماشین ریختهگری تحت نظارت مداوم قرار داشت تا از بروز هرگونه مشکل فرایندی جلوگیری شود. تنظیم خنککاری، برش تختال و تأمین پودر قالب از چالشهای مهم در این زمینه بود و با انجام تستهای اولیه، تنظیم پارامترهای برش و تأمین پودر قالب با مذاکره با شرکتهای تولیدکننده پودر برطرف شد.
امیرحسین مرادی، رئیس کورههای قوس الکتریکی:
تولید تختال زنگنزن ۳۱۶ که حاوی ۳۵ درصد عناصر آلیاژی است، افتخاری دیگر را برای شرکت معظم فولاد مبارکه رقم زد. این مهم حاصل اهتمام ویژه و خودباوری کارکنان ناحیه فولادسازی و ریختهگری مداوم در جهت تولید ذوبهای ویژه است.
منصور سنایینژاد، مهندس فرایند ناحیه فولادسازی و ریختهگری مداوم:
برای تولید این محصول جدید که کاربردهای زیادی در صنایع خورنده دارد، ابتدا همکاران در قسمت دفتر فنی ریختهگری به مطالعه خواص گرید ۳۱۶ ازلحاظ نوع انجماد، استحالههای در حین انجماد، میزان هدایت حرارتی، چگونگی تشکیل پوسته جامد در قالب ریختهگری، میزان انقباض و بسیاری دیگر از پارامترها که تأثیر زیادی در نحوه طراحی فرایند ریختهگری دارند پرداختند و سپس با توجه به اطلاعات بهدستآمده طراحی فرایند انجام شد و پارامترهای کنترل دما، سرعت، میزان شیب قالب، جداول آب ثانویه و اسیلاتور و سایر پارامترهای موردنیاز فرایند ریختهگری را با واحد تولید ریختهگری به اشتراک گذاشتند. همچنین با توجه به اینکه ساختار آستنیتی مناسب در حین ریختهگری یکی از پارامترهای بسیار مهم در تولید این گرید است هماهنگی لازم با واحدهای تولید مذاب و متالورژی ثانویه جهت کنترل آنالیز شیمیایی برای به دست آمدن ساختار مناسب انجام پذیرفت.
بهنام ادیبی، کارشناس تولید کورههای الکتریکی:
فولاد زنگنزن گرید ۳۱۶ بهواسطه ترکیب شیمیایی ویژه خود، یکی از فولادهای زنگنزن مقاوم به انواع خوردگی، بهخصوص خوردگی حفرهای است و بهصورت لوله و ورق کاربرد بسیار زیادی در صنایع فرایندی مختلف دارد.
محمد عظیمی، شیفت فورمن متالورژی ثانویه:
امروزه تولید فولادهای خاص با ارزشافزوده بالا ضامن حیات شرکتهای تولیدی محسوب میشود. تولید این فولاد در مرحله کوره قوس منجر به افزایش کربن میشود. کاهش کربن در محدوده مجاز به کمک دمش اکسیژن و ایجاد محیط خلأ و بازیابی فروکروم اکسیدشده از سرباره بهعلاوه تنظیم نهایی آنالیز شیمایی و دمای مناسب این ذوبها، در فرایند RH انجام میگیرد. چالش اصلی تولید این فولاد به کمک RH دسترسی محدود به سطح سرباره و انجام عملیات بر روی سرباره است که با برنامهریزی مناسب این مهم در شرکت فولاد مبارکه در واحد متالوژی ثانویه و قسمت RH محقق گردید.
حسین محمد قاسمی، هماهنگکننده ناحیه فولادسازی و ریختهگری مداوم:
سومین ذوب فولاد زنگنزن با گرید جدید a316 در ناحیه فولادسازی و ریختهگری با موفقیت قابلقبولی تولید شد. تولید این گرید پرکاربرد تجاری و صنعتی با بیش از ۳۵ درصد عناصر آلیاژی، نویدبخش افزایش سهم محصولات با ارزشافزوده زیاد، در سبد تولیدات آینده فولاد مبارکه است. ارتقای جایگاه فنی و دانشی شرکت نیز از برکات تولید این محصول و محصولات مشابه در گذشته است.
فرزاد تیموری، کارشناس فرایند ناحیه فولادسازی و ریختهگری:
فولادهای زنگنزن (Stainless Steels) گروه وسیع و پرکاربردی از فولادها هستند که برای مقاومت در برابر انواع خوردگیها توسعه یافتهاند. عنصر پایه و اصلی آلیاژی در این فولادها که باعث ایجاد خاصیت زنگنزن بودن میشود، کروم است که حداقل ۱۱ درصد در ترکیب آنها وجود دارد.
فرایندهای رایج فولادسازی با تمرکز بر احیای اکسیدهای آهن و افزودن عناصر پایه آلیاژی مثل سیلیسیم و منگنز طراحی شدهاند که خط تولید به کار گرفتهشده در شرکت فولاد مبارکه نیز با محوریت تولید فولادهای ساده کربنی و کمآلیاژ اجرا شده است و این موضوع اهمیت تولید گریدهای فولاد زنگنزن در فولاد مبارکه را دوچندان میکند.
کورههای موجود در شرکت دارای سیستم تخلیه از کف (EBT) بوده و افزودن مقادیر زیاد کروم که یک عنصر مستعد اکسید شدن در حضور اکسیژن است، بهدلیل ایجاد مشکل در تخلیه کوره یکی از مشکلات عمده تولید فولاد زنگنزن در فولاد مبارکه بود که با همت و اندیشه کارکنان متخصص فولاد مبارکه راهکار مناسب جهت جلوگیری از کاهش بازده جذب فروکروم در کوره و فرایند تخلیه پیشبینی و با موفقیت اجرایی شد و برای اولین بار یک گرید آلیاژی با حدود ۷۰ تن مواد افزودنی آلیاژساز با موفقیت در کوره قوس الکتریکی فولاد مبارکه ذوبسازی و تخلیه گردید.
نکته مهم دیگر در تولید گرید آستنیتی ۳۱۶ کاهش کربن در واحد RH و سپس احیا کروم اکسیدشده در فرایند کربنزدایی بود؛ چراکه انجام این فرایند با توجه به شرایط متفاوت سرباره حاوی اکسید کروم دارای سختیها و مشکلات فراوان است؛ اما خوشبختانه این مرحله از تولید نیز در شرکت فولاد مبارکه با موفقیت طراحی و اجرا شد.
تنظیم دمای مناسب برای ارسال به ریختهگری با توجه به افزایش شدید دما حین فرایند کربنزدایی و احیای سرباره از دیگر نکات مهم در این زمینه بود. در انتها ریختهگری بدون عیب با وجود تفاوت زیاد در خواص حرارتی و سیالیت این گرید آستنیتی دارای مولیبدن برای اولین بار بهصورت ریختهگری مداوم انجام شد و این مهم با تنظیم دقیق جداول آب، سرعت ریختهگری، حالت نوسانگر و استفاده از پودر قالب مناسب محقق شد.